目次
前言
引言
1 范围
2 规范性引用文件
3 术语和定义
4 分类
5 技术要求
6 试验状态
7 试验方法
8 标志
9 制造商提供的信息
附录A(规范性附录) 耐磨性试验方法
附录B(规范性附录) 抗切割性试验方法
附录C(规范性附录) 抗撕裂性试验方法
附录D(规范性附录) 抗刺穿性试验方法
附录E(规范性附录) 耐接触热试验方法
附录F(规范性附录) 耐对流热试验方法
附录G(规范性附录) 垂直电阻测量的试验方法
附录H(规范性附录) 抗切割性试验用帆布比对试样的其他技术要求
前言
本标准代替LD 34.3—1992《焊工手套》。本标准修改采用欧洲标准EN 12477:2001+A1:2005~焊工防护手套》(英文版)。本标准根据EN 12477:2001+A1:2005重新起草。
本标准根据GB/T 1.1—2000的规则,设置第3章“术语和定义”和第4章“分类”,将EN 12477:2001+A1:2005中“范围”一章之后的术语和定义归集到此第3章中,分类归集到此第4章中。因此,本标准自第4章以后的章编号是在EN 12477:2001+A1:2005的章编号上加2。例如,EN 12477:2001+A1:2005中的第3章,在本标准为第5章。
本标准与EN 12477:2001+A1:2005相比,存在如下少量技术性差异:
——将欧洲标准的格式和表述转化为我国标准的格式和表述,根据汉语习惯进行了编辑性修改,使语言表述更精练、更通顺;
——EN 12477:2001+A1:2005中引用的相关欧洲标准,在本标准中尽可能将其转化成国内相关标准,对暂无对应国内标准的欧洲标准,本标准将其翻译并作了一些修改后加到相应条款中或作为附录附后;
——本标准用EN 388:2003《机械性危害防护手套》和EN 407:2004《热危害(热和/或火)防护手套》分别代替了EN 12477:2001+A1:2005中引用的EN 388:1994和EN 407:1994;
——在7.5“燃烧特性”条款中,内容由EN 407:2004的6.3翻译过来,本标准将其中的试验点火时间分别用3 s和15 s修改为仅用15 s;
——附录G由EN 12477:2001+A1:2005中引用的EN 1149—2:1997翻译过来,本标准将EN 1149—1:2006的相关内容代替了其中引用的EN 1149—1:1995的内容。
为了便于使用,本标准还对EN 12477:2001+A1:2005做了下列编辑性修改:
——用小数点符号“.”代替小数点符号“,”;
——删除了EN 12477:2001+A1:2005的前言,修改了EN 12477:2001+A1:2005的引言;
——将表2“A类抗刺穿性”指标的印刷错误“670 N”改正为“60 N”。
本标准与LD 34.3—1992相比主要变化如下:
——修改了分类及标记(本标准的4;LD 34.3—1992的3);
——删除了外观和厚度要求(LD 34.3—1992的4.1.1和4.1.2);
——修改了尺寸的要求(本标准的5.2;LD 34.3—1992的4.2.4);
——修改了技术性能要求(本标准的5.3和5.4;LD 34.3—1992的4.1.3~4.1.5);
——删除了制作工艺要求(LD 34.3—1992的4.2);
——增加了试验状态要求(本标准的6);
——修改了试验方法(本标准的7和附录A~附录H;LD 34.3—1992的5);
——删除了检验规则(LD 34.3—1992的6);
——修改了标志要求(本标准的8;LD 34.3—1992的7.1);
——删除了包装、运输、贮存要求(LD 34.3—1992的7.2~7.4);
——增加了制造商提供的信息的要求(本标准的9)。
本标准的附录A、附录B、附录c、附录D、附录E、附录F、附录G和附录H为规范性附录。
本标准由国家安全生产监督管理总局提出。
本标准由全国个体防护装备标准化技术委员会(SAC/TC 112)归口。
本标准起草单位:上海市安全生产科学研究所。
本标准主要起草人:邵宝仁、梅灿华、唐一鸣、蒋瑞靓、王桂芬、尹建国。
原标准LD 34.3—1992于1992年4月首次发布。
引言
欧洲标准化委员会防护服(包括手臂防护和救生衣)技术委员会CEN/TC 162于2001年制定了EN 12477《焊工防护手套》,并于2005年发出了第1份修改单A1对其进行了修订。EN 12477:2001+A1:2005现已在英国、法国、德国等二十七个欧洲国家贯彻执行。为了适应标准化工作的需要,进一步与国际先进标准相协调,促进贸易与交流,修改采用EN 12477是必要的。
焊工防护手套
1 范围
本标准规定了在手工金属焊接、气割和类似作业中使用的防护手套的要求和试验方法。
本标准适用于在焊接和相关的作业过程中对手部和腕部起保护作用的焊工防护手套。
本标准不适用于特殊焊接作业使用的防护手套。
2 规范性引用文件
下列文件中的条款通过本标准的引用而成为本标准的条款。凡是注日期的引用文件,其随后所有的修改单(不包括勘误的内容)或修订版均不适用于本标准,然而,鼓励根据本标准达成协议的各方研究是否可使用这些文件的最新版本。凡是不注日期的引用文件,其最新版本适用于本标准。
GB/T 5456--1997 纺织品 燃烧性能 垂直方向试样火焰蔓延性能的测定(eqv ISO 6941:1992)
GB/T 12624--2006 劳动防护手套通用技术条件(ERr 420:2003,Protective gloves—General requirements and test methods,MOD)
GB/T 16839.1—1997 热电偶 第1部分:分度表(idt IEC 584—1:1995)
GB/T 17599--1998 防护服用织物 防热性能 抗熔融金属滴冲击性能的测定(eqv ISO 9150:1988)
GB/T 19089--2003 橡胶或塑料涂覆织物 耐磨性的测定 马丁代尔法
SN 0704—1997 出口皮革手套中铬(Ⅵ)的检验方法 分光光度法
3 术语和定义
下列术语和定义适用于本标准。
3.1
焊工防护手套 protective gloves for welders
保护手部和腕部免遭熔融金属滴、短时接触有限的火焰、对流热、传导热和弧光的紫外线辐射以及机械性的伤害,且其材料具有能耐受高达100 V(直流)的电弧焊的最小电阻的这样一种手套。
注:这并不意味在误用或错用焊接设备的情况下焊工防护手套能提供任何保护,也不证明在本应使用按GB 17622设计的防护手套的地方使用焊工防护手套能防止电击。
4 分类
焊工防护手套按照其性能分为两种类型:
——A类:低灵活性(具有较高的其他性能);
——B类:高灵活性(具有较低的其他性能)。
5 技术要求
5.1 一般要求
焊工防护手套除其长度应按5.2规定外,其余都应符合GB/T 12624--2006中4.1和4.2规定的要求。
皮革制手套中铬(VI)含量应低于3 mg/kg。从每一皮革类型中不同的手套上至少取2个试样,铬(Ⅵ)含量按SN0704—1997中规定的检验方法测定。若手套由不同类型的皮革制成,每一类型的皮革不管其接触皮肤与否,都应进行试验,最终结果取最高值。
5.2 尺寸
尺寸按GB/T12624—2006中5.2.3和5.2.4测量,应符合GB/T12624—2006中4.3.1.2规定的要求,但最短长度应符合表1的规定。

5.3 特殊要求
焊工防护手大旱应按照表2的规定进行试验,并根据试验结果进行A类和/或B类的分类。

在每一项热试验后,所有的内部材料都应经过检查,以确认没有熔融发生。
在燃烧特性试验时,经规定的点燃时间后,试验部位的接缝不应分开。
在抗熔融金属滴冲击性试验时,若熔滴粘附在材料上,则材料应不点燃。
5.4 在正常使用条件下用于电弧焊的手套的附加要求
手套不应设计成其外部和内材之间的导电连接,例如用铆钉那样的金属部件来连接。用外观检查来检验其符合性。
A类和B类手套的垂直电阻应大于10
5Ω。试验按7.10进行。
6 试验状态
在试验前,试样应按指定的试验方法标准中的规定进行预处理。
若规定了保养指南,则手套在清洁之前和受到所建议的最多清洁次数之后应都进行全部的试验。
7 试验方法
若受到试验的手套部位是由不同的材料组成,则所有这些材料都应进行试验,分类按获得的最低性能等级而定。
7.1 耐磨性
焊工防护手套的材料应按附录A进行试验,试验部位为手套的掌部以及背部(当两者是不同材料时)。
7.2 抗切割性
焊工防护手套的材料应按附录B进行试验,试验部位为手套的掌部。
7.3 抗撕裂性
焊工防护手套的材料应按附录C进行试验,试验部位为手套的掌部。
7.4 抗刺穿性
焊工防护手套的材料应按附录D进行试验,试验部位为手套的掌部。
7.5 燃烧特性
手套试验方法应按GB/T 5456—1997进行,其中作如下规定和修改:
——试样的调湿按GB/T 5456—1997中7.4.1的规定进行,至少24 h。
——手套垂直安装,使A点(图1)位于下边缘的中点;

——把点火器放在手套下面,位于手套或中指垂直中心线平面内,并垂直于手套表面。点火器的放置与垂直线成(30±3)°的夹角。点火器顶端与手套或中指下边缘间的距离应为(20±2)mm;
——点火时间为15 s,用一只手套进行试验,试验的续燃时间和阴燃时间应记录。
7.6 耐接触热
焊工防护手套的材料应按附录E进行试验,试验部位为手套的掌部,接触温度为100℃。
试样直径为80 mm,从三只手套的掌部取得。
所有单个t
t值应符合表2中要求的最低性能。结果应以三个值的算术平均给出并修约到整数位秒。
7.7 耐对流热
焊工防护手套的材料应按附录F进行试验,试验部位为手套的掌部以及背部和袖筒(当三者是不同材料时)。每一种材料或每一种材料组合应试验三个试样,所有单个值应符合表2中要求的最低性能。结果应以三个值的算术平均给出并修约到整数位秒。
7.8 抗熔融金属滴冲击性
焊工防护手套的材料应按GB/T 17599—1998进行试验,试验部位为手套的背部以及袖筒(当两者是不同材料时)。
试样尺寸为120 mm×20 mm,从四只手套的背部取得。
所有单个值应符合表2中要求的最低性能,试验结果应以四个值的算术平均给出并修约到整数位。
7.9 灵活性
手套应按GB/T 12624--2006中5.3进行试验。
7.10 在正常使用条件下用于电弧焊的手套的试验一垂直电阻
焊工防护手套的材料应在温度为(20±2)℃和相对湿度为(85±3)%的大气环境中至少放置24 h,试验在这样的环境下或离开这样的环境5 min之内按附录G进行。
防护手套(包括袖筒)的每一不同部件的垂直电阻都应进行试验。若手套的外表面本身超过了要求,则仅需对不同的外表面进行试验;若外表面没有通过,但外表面和衬里的组合符合要求,则手套和袖筒的每一不同结构应进行试验。
8 标志
标志应符合GB/T 12624--2006中6.1和6.2的要求。另外,在每只手套上应标注现行标准号,后跟字母A或B(依据该手套是A类还是B类产品而定),再加上热危害和机械危害的图案。
从清洁之前或最多清洁次数之后获得的最低性能等级应在标志中标注。
在每个手套的直接包装上应标注热危害防护手套的图案以及本标准号和手套的类型。
制造商也可选择在每个包装上附加一个机械危害防护手套的专门图案。
9 制造商提供的信息
使用说明应符合GB/T 12624--2006中6.1和6.3规定的要求。
从清洁之前或最多清洁次数之后获得的最低性能等级应在使用说明中写明。
制造商应给出手套使用方面建议的信息。
当要求高灵活性时,如钨极惰性气体保护焊,建议使用B类手套;对于其他焊接作业建议使用A类手套。
制造商应说明:
——目前没有标准化试验方法来检测手套材料的紫外线穿透,但现行焊工防护手套结构通常不会发生紫外线辐射的穿透。
——用于电弧焊手套不能对由于故障设备或带电作业引起的电击提供保护;若手套潮湿、脏污或汗水浸透,其电阻会降低,这将增加危险。
附 录 A
(规范性附录)
耐磨性试验方法
A.1 原理
在已知压力下,材料圆形试样以相互垂直的两个简谐运动合成的李萨如(Lissajous)图形方式在平面上进行循环摩擦运动。
耐磨性是由磨损破坏出现的圈数决定的。磨损是指在试样上出现一个破损的小洞。
A.2 磨料
A.2.1 磨料应满足以下要求:
a) 衬背:衬背应为一合适质量,即至少为125 g/m
2±5%的纸张;
b) 粘合剂:粘合剂应为水溶性的,质量好并适用;
c) 研磨剂:所用玻璃砂应质量好,适用并能满足表A.1所给筛选分析要求。

A.2.2 所完成的玻璃砂纸应有以下特性:
a) 破裂强度应不小于:
——机械加工方向:392 N/50 mm:
——横向:215 N/50 mm。
b) 玻璃砂纸的重量应为300 g/m
2±10%。
A.3 装置
GB/T 19089--2003中4.1所描述的磨耗试验机,并应达到试样所受压强为(9±0.2)kPa的要求。
A.4 试样
应从同一手套系列中的四个单独手套中取四个试样。
如果试样是由几层未粘合的材料组成,试验应对每层材料进行。等级的确定应基于各层材料的磨耗圈数之和而定。
A.5 试验步骤
A.5.1 一般要求
设定机器。
检查顶板和摩擦台是否平行。在心轴轴承插入一个千分表,并用手转动传动轴来移动顶板。千分表指针应在摩擦台的整个表面上方±0.05 mm范围内移动。
如果机器的试样架和砝码用心轴连接,则对每个空试样架进行组装,并将它们放在摩擦台的适当位置上,然后插入心轴。用测隙规检查试样架嵌入件表面和摩擦台之间的间隙,间隙不应超过0.05 mm。摇晃心轴,用测隙规再次检查。为了避免损坏摩擦台和金属嵌入件,在金属嵌入件和未覆盖的摩擦台接触时,不可开动试验装置。
A.5.2 安装试样
在试验装置底部的安装板上放置试样架的圆环。将试样置于金属嵌入件之上并对中,用双面胶带将其仔细固定,使之不产生张力,同时使之承受10 kg的压力5 min。使用双面胶带能达到良好的粘合效果,可以防止试样的松动和气泡的产生。
当确定了装有试样和金属嵌入件的圆环被紧密固定在安装板上后,将试样架的上部旋到圆环上,注意旋转螺纹没有转过头。拧紧开始后,对着安装板用双手给组件一个持续向下的压力。
这个步骤通常可以保证试样确定地安装在试样架上不起皱,同时试验可以进行了。
A.5.3 安装磨料
仔细用双面胶带安装磨料。在磨料的表面放上试验机所配备的砝码压平磨料,然后放置保持框并按次序用对角螺丝旋紧的方式均匀将其紧固。确信磨料被牢固定位且没有任何褶皱。
A.5.4 安装试样架
将试样架安装在顶板上,并给予(9±0.2)kPa压力,然后开动试验机。
每次从机器上取下试样架检查试样受试部位的磨损情况后,在重新装上机器前应再次紧固试样架。
若必须中断试验较长一段时间(例如整夜或整个周末),应将试样从试样架中取出,并将其表面朝上存放,再将一张干净的卡片或织物遮盖其上以起保护作用。
A.5.5 评价方法
每次试验都应使用新的磨料。在开始试验100圈后检查试样,如果没有磨损,则继续试验到500圈(性能等级2)。如果仍没有磨损,继续试验至达到下一个性能等级。在每个性能等级所要求的磨耗圈数达到时检查试样。
在规定的性能等级处每次进行试样检查时,试样和磨料都应用干净压缩空气(举例)进行清洁,试样架在重新装上机器前应紧固。
如果在某一个性能等级检查试样时发现磨损,所确定的等级应为前一个低的性能等级。
当磨损出现在一个试样边缘2 mm范围内或者出现撕裂,该试样必须被舍弃,并且重新进行全部试验。如果在第二次试验中,有至少一个试样试验失败时,两次试验中有效试样的最低值作为试验记录。
附录B
(规范性附录)
抗切割性试验方法
注:本试验不适用于以类似锁子甲的非常硬的材料制作的手套。
B.1 原理
试样被一在规定的负荷下往复运动,同时作逆向旋转的圆形刀片切割。
B.2 设备

设备(图B.1、图B.2和图B.3)包括以下部分:
a) 一个圆形旋转刀片水平往复运动的测试台。水平运动距离为50 mm并且刀片的旋转与其运动方向完全相反。产生的刀片最大正弦切割速度的最大值为10cm/s;
b) 加在刀片上产生(5±0.05)N压力的质量块;
c) 圆形刀片直径(45±0.5)mm,厚度(3±0.3)mm,总切割角在30°~35°之间(见图B.3)。刀片应为钨纲所制,硬度在740HV~800HV之间;
d) 放置试样的导电橡胶(硬度(80±3)IHRD)支撑架;
e) 如图B.1所示的试样夹持框;
f) 检测割穿时刻的自动装置系统;
g) 校准精度为0.1周的周数计数器。
B.3 试样
每条试样宽为(60±6)mm,长为(100±10)mm,由斜裁取得。如果试样是由几层未粘合的材料组成,应对包括所有层面材料在一起的完整试样进行试验。
每个手套系列应取两个试样。
B.4 比对试样
比对试样的尺寸与测试的试样一样。比对试样为棉帆布,其技术要求在B.5中给出。
B.5 帆布
织物经纱和纬纱:由开口端纤维纺成的棉纱;
经纬纱线密度:161 tex;
经向复纱:双股S捻280 t/m;
单纱:z捻500 t/m;
纬向复纱:双股S捻280 t/m;
经纱:18纱/cm;
纬纱:11纱/cm;
经缩:29%;
纬缩:4%;
经向拉伸强力:1400 N;
纬向拉伸强力:1000 N;
单位面积质量:540 g/m
2;
厚度:1.2 mm。
对着经向斜裁比对试样。其他的技术要求见附录H。
B.6 试验方法
在橡胶垫上放一张大约0.01 mm厚的铝箔,其上覆盖一张(65±5)g/m
2且不超过0.1 mm厚的滤纸。该纸的目的是为了在测试中固定试样,同时避免检测到由于某些织物中存在钢丝或薄针织物结构间的缝隙而导致的意外割穿。在夹持框中比对试样应不受张力地放在铝箔的上面。
夹持框固定于台上,持刀臂下降至比对试样上。
在试验前,按如下所述检查刀片的锋利程度:在比对试样割穿时,记录周数(C)。如果所预期的性能等级小于3,则周数应在1和4之间,如果所预期的性能等级等于或大于3,则周数在1和2之间。
如果周数少于1,应通过在三层比对织物或任何合适的抗切割材料上进行切割移动来降低刀片的锋利程度。
试样用同样方法进行试验,并记录周数(T)。
每个试样进行五次试验,每次试验按照下列顺序进行:
a) 在比对试样上试验;
b) 在试样上试验;
c) 在比对试样上试验。
如果结果处于两个性能等级之间,试验应用新的刀片重新进行。记录最低的平均值。
对于高抗切割材料,如果在第一个顺序完成后比对试样的周数显示大于3的话,刀片应更换。该顺序应重复两次,每次用新的刀片,指数i的计算根据B.7进行。最终的指数值(I)取两个试样试验结果的最小值。
B.7 试验结果的计算
结果应按照表B.1给出。

表示在试样切割T
n前后比对试样周数的平均值,其计算按下式:

每个试样的最终指数值I按下式计算:

式中:

如果T=0,I的最小值为1。I是一个没有单位的数字。
报告应给出10个i
n结果。性能等级由两个计算所得指数的最低值确定。
附 录 C
(规范性附录)
抗撕裂性试验方法
C.1 原理
抗撕裂性定义为在一矩形试样上撕裂所需的力,矩形试样事先被沿着其长度方向切开一半长度的切口。
C.2 设备
应使用配备有低惯性力测量系统的拉力试验机。
C.3 试样
试样尺寸如图C.1所示。试样尺寸为(100±10)mm×(50±5)mm。在试样纵向距边缘(25±2.5)mm处切一(50±5)mm长的切口。切口的最后1 mm应使用锋利的新刀片切割笔直并与试样表面垂直。

C.4 安装试样
每一经预切割而成的细条(图C.2)应至少有20 mm的部分由拉力试验机的夹具夹持。夹具间的距离至少有10mm,以保证拉力方向与试样纵向平行。

C.5 试验方法
C.5.1 撕裂力用X—Y记录装置记录。拉伸速度为(100+10)mm/min。试样应完全被撕裂为两半。注意在某些情况下撕裂可能不是沿着试样的纵向。
C.5.2 如果试样在超过75 N的力时还没有被完全撕裂为两半,则试验可以停止,然后记录所达到的最大的力。
C.5.3 同一手套系列应取四只不同手套各取一个试样进行试验。如果试样是由几层未粘合的材料组成,则试验应对每层材料进行,等级按获得的最高值确定。
C.5.4 两个试样应以手套方向即从袖筒至指尖方向试验,另两个试样应以横跨掌部宽度方向试验(图C.3)。

C.5.5 每个试样的抗撕裂性取记录的最高峰值。等级则按四个值的最低值确定。
附 录 D
(规范性附录)
抗刺穿性试验方法
D.1 原理
抗刺穿性用一规定尺寸的钢钉刺穿固定于夹持装置上的试样所需的压力来定义。该性能不应与细尖物或针所施加的刺穿相混淆。
D.2 设备
设备包括以下部分:
——一台量程从0 N至500 N的低惯性压力器具;
——一个中心位于器具轴线上的钢钉,尖锐程度要求和尺寸,具体见图D.1;
——一个中心与器具轴线重合,用以夹持试样的夹具,具体见图D.2。

D.3 试样
裁取的试样为圆形,直径至少为40 mm,其上的接缝、加强或增厚部位应位于夹持区域和穿孔点之外。在有几层未粘合的材料的情况下,将这些材料叠加在一起进行试验。
D.4 试验方法
D.4.1 将试样外表面对着钢钉,固定在夹具中央。
D.4.2 将钢钉以100 mm/min的速度向下移动,直到试样延伸至50 mm处。不论试样是否刺穿,记录最高力值。
D.4.3 同一手套系列应从四只不同手套上取四个试样进行试验。
D.4.4 每次试验的钢钉外形和尺寸应符合图D.1要求。对于大部分材料,建议至少每使用500次检测一次钢钉,但对于会损伤钢钉的硬质粗糙的材料,必须增加检测钢钉的次数。
D.4.5 性能等级由记录的最低值确定。
附 录 E
(规范性附录)
耐接触热试验方法
E.1 定义
本附录采用下列定义。
E.1.1
接触温度T
c contact temperature
保持恒温的加热体接触面积的表面温度。
E.1.2
时间测量的开始 start of the time measurement
热量计上表面与加热体底面靠近至10 mm的瞬间。
E.1.3
临界时间t
t threshold time
在时间测量的开始和热量计温度高于其初始值10℃的瞬间之间的时间。
E.1.4
接触速度contacting speed
使加热体和热量计连同试样互相接触的相对速度。
E.1.5
接触力 contact force
当试样和热量计开始与加热体接触时,作用在其上的力。
E.2 原理
把加热体加热到接触温度,并把试样放在热量计上。使加热体下降到由热量计支撑着的试样上,或者,让带着试样的热量计升高至加热体;无论哪种操作方式都应以恒速进行。通过记录热量计的温度,就可确定临界时间。
E.3 装置
E.3.1 加热体
加热体是由能够承受高达超过500℃温度的合适的金属材料制成(例如纯镍)。图E.1所示为一个可行的加热体的形式。接触表面的直径为(25.2±0.05)mm,并应磨光。中间钻孔至加热体的底面之上3 mm。此钻孔为放置温度传感器,用于调节加热体的温度,因此其直径应与传感器的直径相匹配。在加热体的上部加工一个深为D,宽为B,螺距为Z的螺旋槽。应选择尺寸合适的螺旋槽,使得加热导体的全部被加热长度能够放进此槽内。加热体应用一种耐热的绝缘体围封,只露出底部接触表面。

E.3.2 热量计
热量计如图E.2所示,包含一个经黑色阳极化处理的纯铝圆盘,直径(25±0.05)mm,厚(5±0.02)mm,装在由聚酰胺6.6材料做成的支撑托上。热量计的上接触表面在阳极处理前应磨光,在下表面应装上一个温度传感器(例如,铂电阻器)。

E.3.3 组装
图E.3所示为一种可行的组装形式。加热体和热量计安装在支撑架内,面对面平行且对称轴成一直线。应采取措施使加热体朝热量计的下降或热量计朝加热体的上升为可控速度运动。附加配重的尺寸通过接触力为(49±0.5)N来确定。在测量期间,冷却时应在加热体和热量计之间放置一个合适的隔离板,防止热量计受加热体所产生的热辐射的影响。

E.3.4 电子系统
所提供的电子装置应达到下列要求:
——能将加热体加热到至少500℃,并能控制温度;
——能控制接触的速度;
——能测量和记录热量计的温度,精度为±0.1℃;
——能测量临界时间。
E.4 取样和预处理
E.4.1 取样
对于每一接触温度,从产品或打算制造产品的材料上应至少取三个直径为80 mm的圆环试样。
E.4.2 预处理
试验前,试样应在温度为(20±2)℃和相对湿度为(65±5)%的大气环境中至少放置24 h。
E.5 试验方法
E.5.1 开始条件
测量应在温度为(20±5)℃和相对湿度为(15~80)%的大气环境中进行。加热体应被加热至所选择的接触温度±2%(℃)。在每一试验开始之前,热量计的温度应是室温±2℃。试验应在试样从E.4.2规定的预处理大气环境中取出后3 min内开始。
E.5.2 步骤
把试样放在热量计上,外表面朝上。移开在加热体和热量计之间的隔离板,以(5.0±0.2)mm/s的接触速度让加热体接触热量计。测量和记录试验时热量计的温度。每一接触温度至少进行3次测量。
E.5.3 评价
确定临界时间t
t,精确至0.1 s。
附 录 F
(规范性附录)
耐对流热试验方法
F.1 定义
本附录采用下列定义。
F.1.1
试样 test specimen
按实际使用时的次序和取向排列的并包括内衣的所有织物或其他材料层。
F.1.2
入射热通量密度 incident heat flux density
在试样的暴露面上,每单位时间入射的能量,用kW/m
2表示。
F.1.3
热传递指数(火焰) heat transfer index (flame)
当按本方法使用质量为(18.00±0.05)g的铜圆片,初始温度为(25±5)℃试验时,达到温升(24.0±0.2)℃所需的平均时间,单位为秒,再由平均时间取整得到的一个数。
F.2 原理
水平放置的试样部分固定,受到来自于放在其下面的气体燃烧器火焰喷出的80 kW/m
2的入射热通量。通过试样的热量用一个放在试样顶上并与之接触的小型铜热量计测量。
热量计中温升(24.0±0.2)℃的时间用秒记录。三个试样的平均值作为“热传递指数(火焰)”。
F.3 装置
F.3.1 气体燃烧器
平口钢口灯,顶部有孔,直径为(38土2)mm,使用适合丙烷气体的喷嘴。
应使用商品级丙烷,并用精确控制的阀和流量计来控制其流量。
F.3.2 铜片式热量计
热量计为一圆片,其材料为至少99%纯度的铜,直径为40 mm,厚度为1.6 mm,重量为18 g。圆片在组装前应被精确地称量。
如图F.1所示,在铜片上安装一对符合GB/T 16839.1—1997的输出为毫伏的铜一康铜热电偶。康铜丝应被连接在圆片的中心,铜丝应被尽可能地连接在圆周上,但不能影响圆片在安装块上的安装。两种丝的直径应是等于或小于0.26 mm,但与圆片连接的长度应是裸露的。

热量计在安装块中定位。安装块为一直径89 mm的圆板,由无石棉的、非燃的、绝热的标称厚度为13 mm的板制成,其热特性应符合以下要求:
——密度:(750±50)kg/m。;
——导热性:0.18W/(m•k)±10%。
如图F.2所示,在安装块的中央加工一个圆洞,以容纳圆片并提供气隙。用一种能承受约200℃高温的粘合剂沿着圆片的圆周将其粘合定位。铜片的面应与安装块的表面齐平,并且还应薄薄涂上一层吸收系数a大于0.9的光学黑色漆。

F.3.3 试样支撑框
试样支撑框为一铜板,150 mm×150 mm,厚1.6 mm,中间有一个50 mm×50 mm的孔(图F.3)。

F.3.4 热量计定位板
热量计定位板由149 mm×149 mm和6 mm厚的铝板制成。在铝板的中间应有一个直径为
90 mm的圆孔(图F.4)。铝板应重(264±13)g。

F.3.5 支撑架
试样支撑框顶面应在燃烧器顶面上方50 mm处,两个面互为平行,燃烧器的轴线与支撑框开孔中心对准(图F.5)。
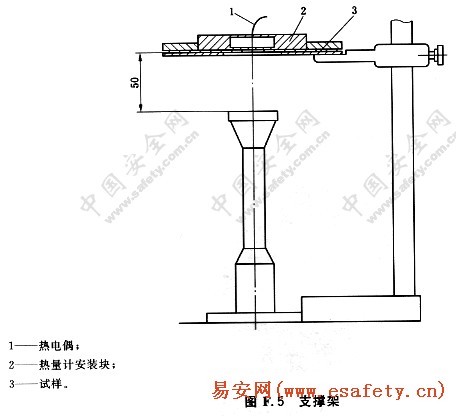
为方便起见,在燃烧器和试样支撑框之间设置一块遮蔽板,其完全打开应小于0.2 s并在燃烧器放置到位后立即动作。如果燃烧器的到位或遮蔽板的打开被配备的话,就能用于自动记录暴露于火焰的开始,那是非常有用的。
F.3.6 记录仪器
为了能确定铜片的绝对温度,热电偶应与冰或商品参考物连接。热电偶发出的电压信号应该被连接到一台合适的电位图表记录器或可编程数据记录器。记录器应该能读出10μV电压和0.2 s时间。
F.3.7 样板
一个刚性平板,尺寸为140 mm×140 mm。
F.4 预防措施
F.4.1 在有排风罩或有通风设施的地方进行试验,以便排出烟气。在试验过程中可能必需关掉排气装置或遮蔽装置,防止扰动火焰。
F.4.2 在试验过程中设备变得发烫,并且某些试验材料可能溶化或滴落。当拿捏热的物体时,带好防护手套。
F.4.3 保持易燃物质远离燃烧器,确保用于清洁热量计的溶剂远离热表面和明火。
F.5 取样
F.5.1 试样尺寸
试样尺寸为(140±5)mm×(140±5)mm,若从手套上裁取这样的试样不可能,则可从材料上裁取,只要其制作与手套相同并包含任何存在的接缝。复合的试样应按照实际使用时的情况排列。
试样应用样板(见F.3.7)划线标出。
F.5.2 试样数量
对每种材料或复合材料至少应试验三个试样。
F.6 预处理和试验大气环境
F.6.1 预处理大气环境
在试验前,试样应在温度(20±2)℃,相对湿度(65±2)%的环境中至少预处理24 h。如果预处理后试验不立即进行,应把预处理过的试样放置在密封的容器中。每一试样从预处理大气环境或密封容器取出后3 min内开始试验。
F.6.2 试验大气环境
应在温度为10℃~30℃,相对湿度为15%~80%,没有气流的大气环境中进行试验。
F.7 试验步骤
F.7.1 准备和校准
F.7.1.1 初步测量
把支撑框放在支撑架上,使放置试样的上表面高于燃烧器顶端50 mm。建议使用一个导向装置和阻挡器,使得燃烧器能在其轴线与试样中心线成一线时迅速定位。
把燃烧器放在一边,开启并点燃气源,等待几分钟让火焰稳定。
将热电偶与冷点连接,并将输出电压连接到记录装置。在每次入射热通量密度调节或试样评价前,铜片温度应该处于相对稳定状态,在环境温度的±2℃之内。可使用任何干燥、能降低温度的吸热器或强迫通风进行加速冷却。可以选择的是许多热量计装置可以旋转。加热则可通过手掌接触铜片或短时间暴露在燃烧器火焰中达到。
注:热量计安装块决不应被允许接触到水。若此意外发生,该安装块在再次使用前应该彻底弄干。
F.7.1.2 入射热通量密度的调节
气流速度和燃烧器的设置会随个别使用的组合而变化,所以在装置安装的初始阶段和试验进行过程中时常需对其中一个或者全部两个的设置进行调整。正确的流量应该这样来判别:一个轮廓分明并且稳定的淡蓝色的锥形固定在燃烧器格栅上,其上有一束大的漫射的蓝色火焰。
通过用热量计测量热通量密度来确认火焰的设置。
把热量计定位板放在样品支撑框上。把热量计铜片面朝下放在定位板的孔中。
选择记录装置所需传送速度,迅速谨慎地滑动燃烧器至热量计下面,直到其在阻挡器处定位。如果使用了遮蔽板,打开遮蔽板(见F.3.5)。让燃烧器在原位保持约10 s。
退出燃烧器或关闭遮蔽板。
所记录的输出应该显示:在刚开始暴露后,一个短的非线性温度一时问区域,随后是一个连续的直到暴露终止的线性区域。参照标准热电偶电动势表,确定线性区域的温升率,单位为℃/s。那么热通量密度Q(kW/m
2)就可从下式确定:

式中:
M一铜片质量,kg;
C
p——铜的比热,0.385 kJ/kg℃;
R——铜片线性区域温升率,℃/s;
A——铜片面积,m。。
这一步骤所确定的热通量密度应该在规定的80 kW/m
2的±5%范围内。如果需要,可以调节气流速度,反复调节,直到三个相邻值都在要求的范围内为止。
F.7.2 试样安装
F.7.2.1 将试样表面最外层朝下放在试样支撑框(见F.3.3)上。把定位板(见F.3.4)放在试样的上面。
F.7.2.2 如果试样的层数超过一层,且层间互不连接,取下定位板,把每一层按使用时组合的次序和取向排列安装。用定位板的重量,不要添加额外的压力,对每一层施压,使其与前面一层接触良好。
F.7.2.3 叠放好最后一层(最里面的)后,重新放上定位板,把热量计放在定位板的孔中,使铜片接触到最里层的上部。
F.7.3 试样的暴露
F.7.3.1 迅速谨慎地滑动燃烧器到位,若配置的话,立即移开试样下的遮蔽板,在试样暴露于燃烧器火焰的同时开启记录装置,或对正在运行的记录仪作暴露开始的标记,用哪一种操作取决于使用的设备。
F.7.3.2 让试验继续进行直到温升达到(24±0.2)℃。在试验中,观察和记录试样外观的变化,例如收缩、烧焦,碳化,穿孔,发光,溶化或滴落。若需配置的话,应重新把遮蔽板移回原处,退出燃烧器,并关掉记录仪。
F.7.3.3 移开热量计,当其还很烫(见F.4.2)的时候清理掉任何燃烧后产生的物质,然后将其冷却到环境温度的±2℃以内。
如果在热量计上的残留物质很厚或者不均匀,如果黑色涂层已损坏,或者出现铜暴露,那么应该清洁热量计铜片,并重新对其油漆(见F.3.2)。在对后面的试样试验前,重新涂层后的热量计应该至少进行一次校准运行过程(见F.7.1.2)。
F.7.3.4 测量热量计温升(24.0±0.2)℃的时间,用秒表示。
F.7.3.5 重复上述步骤对另外两个试样进行试验。计算升温(24±2)℃的时间平均值作为热传递指数,取整数。
注:也可以测量温升(12.0±0.1)℃的时间,用秒表示,相当于使用18.00 g的热量计其热电偶输出增加0.5 mV。这种测量能用来确定热传递减缓或减少到何种程度。然而,应该强调的是:测得的时间精度有限,不一定与实际使用条件下的保护时间相关。
附 录 G
(规范性附录)
垂直电阻测量的试验方法
G.1 定义
本附录采用下列定义。
G.1.1
垂直电阻R
v vertical resistance
用规定的电极确定的通过一种材料的电阻,单位为欧姆。
G.2 试验原理
把两个电极各放在被试材料的正反两个表面,在电极上施加一个直流电压,试验材料的垂直电阻就可确定。
G.3 试验装置
G.3.1 电极组件
G.3.1.1 一般要求
和试验材料的电接触应通过电极组件来建立,该电极组件也确定测量表面形状,如图G.1 所示。
G.3.1.2 试验电极
试验电极包含一个金属圆盘(1),约3 mm厚,直径d
1===50.4 mm,该圆盘被固定在一个分开的高绝缘性材料制成的圆盘(2)之下,与一个金属保护板(3)同心。一个同轴插入接头(4)提供电接触到金属圆盘和金属保护板。
G.3.1.3 环形电极
环形电极包含一个金属保护环(5),约3 mm厚,内直径d
2=69.2 mm,外直径d
3=89 mm,该保护环被放置在一个分开的高绝缘性材料制成的环(6)之下,与一个外直径d
4=100 mm的屏蔽环(7)同心。与屏蔽环(7)绝缘的连接插头(8)的插入提供电接触到金属保护环(5)。
G.3.1.4 底座电极
底座电极包含一个金属圆盘(9),直径(110±0.2)mm,约12 mm厚,在其下面配备一最大厚度为1 mm,绝缘电阻不小于10
14Ω的绝缘层(10)。一个插座(11)提供了电接触。
G.3.1.5 组件的结构
试验电极与环形电极同心放置,且应在环形电极内被方便的移动。为达到电接触,在三个孔(13)内应放入弹簧球。三个孔沿着试验电极金属保护板(3)和环形电极屏蔽环(7)间接触面积的周长等距离分布。另外,弹簧的压力应很小,使得产生的任何额外摩擦力可以被忽略。
与试样接触的电极(1)、(5)和(9)的表面应用相同的材料制作,这样,在万一试样包含有电解质时,不会发生电解连接的情况。
试验和环形电极的总质量应为(1 020±20)g,使之在试验材料上施加一个约为10 N的恒压。为了确保试验和环形电极各具有相等的压力(约0.225 N/cm
2=2.25 kPa),试验电极的质量应为(460±10)g,环形电极的质量应为(560±10)g。
图G.1是一个结构图,图中所示尺寸适合于金属部件用比重为7.8 g/cm
3的钢和绝缘部件用比重约为1.19 g/cm
3的聚甲基丙烯酸甲酯(PMMA)、聚苯乙烯(PS)和聚碳酸酯(PC)制作的组件。

G3.2 电阻计或静电计
电阻计量程为(10
5~10
14)Ω。量程≤10
12Ω时,误差范围在±20%。
另外也可选用静电计,其输入阻抗不小于10
14Ω,并配备一个分开的具有内置安全电阻器的直流电源。
G.3.3 电极清洁剂
使用合适的清洁剂,例如2一丙醇或乙醇。
注:有些认为合适的清洁剂,如2一丙醇或乙醇极易燃烧并有毒。为避免燃烧、蒸汽的吸人以及这类产品与皮肤、眼睛和服装的接触,建议采取适当的集体或个体防护措施。
G.4 试样或样品/衣服和预处理
G.4.1 试样或样品/衣服
从样品或者衣服上裁取五个试样,每个的尺寸在环形电极和底座电极的最大尺寸之间。如果是对样品/衣服进行试验,则测量应在五个不同的合适部位进行。手拿试样的时候要放在边上避免污染。
注:当防护服交付样品的制造材料已被使用过时,试样可从相同的生产批次中取得。
G.4.2 预处理和试验大气环境
试样或样品/衣服在试验前应进行至少24 h的预处理,其预处理和试验应在如下大气环境中进行:
——空气温度:(23±1)℃;
——相对湿度:(25±5)%。
注:为特定的目的,可以要求其他大气环境。
G.5 试验步骤
G.5.1 清洁
通过用纸巾蘸上一种清洁剂擦拭的方式来清洁试验和环形电极的下表面以及底座电极的上表面(见G.3.3)。
G.5.2 底座电极的绝缘试验
按G.5.3.3给出的步骤但不放试样进行空白试验。计算绝缘层的电阻系数,并核对其是否符合G.3.1.4 的要求。
G.5.3 试验
G.5.3.1 底座电极的非绝缘面应朝上放置。试验材料应放置在底座上,随后试验电极和环形电极则应同心放置在试验材料之上。线路构成如图G.2所示。

G.5.3.2 如果试验样品测得的表面电阻系数小于10
8Ω,应只对试样而不对样品/衣服进行试验,并在测定R
v时不应将金属保护环(5)接地,因为不是这样的话,非常高的故障电流会引起试验电压的过度降低。表面电阻系数测量按图G.3所示连接电极,施加一个(100±5)V的电压,在(15±1)s后用电阻计测量电阻,并用下列公式计算表面电阻系数ρ:
ρ=k×R
ρ——计算的表面电阻系数,Ω;
R——测得的电阻,Ω;
K——电极的几何系数,在此为19.8。

G.5.3.3 施加一个(100±5)V的电压,在(15±1)s后用电阻计或静电计测量垂直电阻。如果垂直电阻小于10
5Ω,可以施加一个适当的低电压,但应在试验报告中说明。
G.5.3.4 若有必要的话,小于10
5Ω的垂直电阻可采用先测量通过一个与试样成串联的合适安培计的电流,然后计算施加电压与测得电流的比值这样的方法来确定。
G.5.3.5 对其他四个试样或衣服上四个不同的部位重复这一步骤。
G.6 计算和结果表达
计算五个垂直电阻测量值的算术平均值。
附录H
(规范性附录)
抗切割性试验用帆布比对试样的其他技术要求
H.1 一般要求
表H.1列出了抗切割性试验中用作比对试样的棉帆布的其他特性和技术要求,抗切割性试验见附录B。
这些数字值是用世界著名的KESF[川端康成(Kawabata)织物评价系统]的方法和仪器得出的。
使用的棉纱聚合度为2000±50。

H.2 KESF:川端康成(Kawabata)织物评价系统
H.2.1 拉伸
拉伸循环,最大拉伸应力极限为-9.8N/cm。
LT:线性(表征弹性,一次拉伸);
WT:拉伸能量,J/m;
RT:回弹性,即恢复能量的百分比。
H.2.2 弯曲
垂直放置样品上的交替弯曲循环。
B:弯曲韧性;
2HB:1 cm
-1曲率的弯曲迟滞。
H.2.3 剪切
将矩形样品交替变形为角度为8。的平行四边形。
G:剪切韧性;
2HG和2HG5:0.5与5度变形的剪切迟滞。
H.2.4 压缩
厚度压缩循环,最大极限为5.0 kPa。
LC:线性(表征弹性,一次压缩);
WC:压缩能量,J/m
2;
RC:回弹性,即恢复能量的百分比。
H.2.5 表面特性
用25 mm。(摩擦系数)和5 mm宽(粗糙度)的传感器表征一个表面。
MIU:摩擦系数的平均值;
MMD:摩擦系数的平均偏差;
SMD:表面粗糙度的平均值,单位为μm。